Thrives in the harshest conditions that defeat Natural rubber, SBR and Butadiene
EPDM Compounds also deliver higher energy efficiency with a minimal environmental footprint.
Ethylene Propylene Diene Monomer EPDM is a saturated polymer chain of the polyethene type, consisting of ethylene, propylene, and diene. It is one of the most widely used and in-demand synthetic rubbers.
We have expanded the range of EPDM products available through Continued Technology development driven by novel catalysts and process innovations.

Broad Overview of recent developments in EPDM Product Technology
Discover the possibilities of polymer chemistry and physics, characterisation, applications, and manufacturing EPDM products.
What makes EPDM Compounds so tough?
EPDM Compounds have superior heat resistance because the molecules of EPDM have an utterly saturated hydrocarbon backbone, enabling excellent ozone resistance and heat and oxidation resistance.
Choose the EPDM Compound to suit your Application
Choose by Molecular Weight
EPDM Products chosen by molecular weight can be subdivided into three broad categories | ||
---|---|---|
Low-medium viscosity | ML (1 + 3) 100°C-in the range 25-60 | Low-viscosity polymers are preferable for good-quality compounds with moderate filler content. |
Medium-high viscosity | ML (1 + 4) 125°C-in the range 60-100 | Some compounds in this group types contain a certain amount of oil to ease processing. High viscosities are useful to produce low-cost compounds or for improved processability |
Very high viscosity | ML (1 + 4) 125°C-up to 200 (nominal) | Those of type (c) is always oil extended |
The Possibilities & the Difficulties
Processibility & Extrudability
With increased molecular weight measured by Mooney viscosity, we can mix compounds with increased green strength (leading to better tear strength), tensile strength, increased cross-linked density and better thermal resistance. However, despite several advantages, we may experience difficulty in processability and Extrudability.
New materials, Increased Choices
Today, with a broad range of materials available, we have choices of materials with even broadened molecular weight distribution providing ease in processability (Reduced compound Mooney), Calendaring (Elasticity), Extrudability (Reduced die swell), and higher elongation (with a reduced rate and state of cure and evident decrease in tensile strength)
The Role of Ethylene Content
- Increased ethylene increases its crystallinity, higher cold green strength, and higher tensile strength, with advantages in filler loading.
- The ethylene content of commercial ethylene-propylene-diene rubber is between 45 and 75 per cent. Grades with an ethylene content of 45 to 55 per cent weight are amorphous and offer the best low-temperature flexibility.
- EPDM grades with an ethylene content of 55 to 65 per cent are partially crystalline. When the ethylene content rises, the crystallinity increases too.
- Terpolymers containing more than 65-weight per cent ethylene have larger crystalline regions and behave like thermoplastic elastomers. Even in the uncured state, their tear strength is very high.
- The diene content of commercial products is between 2 and 12 per cent. This corresponds to 3 to 16 double bonds per 1000 carbon atoms. A higher diene content leads to a higher crosslinking rate, higher strength values and lower permanent deformation. By contrast, the weathering, ozone, and ageing resistance drops as the diene content increases.
Unsaturation Level
The third monomers currently being used, as already mentioned, are ethylidene norbornene (ENB), 1,4-hexadiene (1,4-HD) and dicyc1opentadiene (DCPD).
According to their third monomer content, EPDMs can be classified into three groups | |
---|---|
Medium unsaturation content of 3-5 % in weight | Medium unsaturation polymers are those currently used in standard compounds and applications. |
High unsaturation content of 5-7 % in weight | The higher unsaturation polymers are more suitable for blending with unsaturated rubbers or giving particularly short curing cycles |
Very high unsaturation content of 8-10% in weight | Compounds mixed with EPDM polymers with increased ENB result in better cure rate, cure state, modulus, hardness, and elasticity.It also gives us flexibility in using accelerators; at the same point, we do observe a decrease in heat resistance, ozone resistance and scorch safety |
Characteristics of our EPDM Compounds
- Our compound can have a reasonably wide operational temperature range of -50 °C to +150 °C.
- It's suitable for sub-zero environments and cold materials. In addition, it offers outstanding weathering properties, including excellent ozone and sunlight resistance.
- It delivers excellent tear, abrasion, and steam resistance and good resistance to compression set, dilute acids, ketones, and alkalis.
- Its widely used as a lower-cost polymer thanks to its comprehensive capabilities and good processing abilities.
- It has excellent water resistance, fresh and salt, and is very good with ozone, UV and oxidation.
- It has moderately high flame and cold resistance, with very high flexibility. Moderately stretchy
EPDM Applications across different industries
Construction Industry
EPDM Compounds are used in weatherproofing and waterproofing, especially on roofs. It is also used as a sealant for garage doors, expansion joints, and a liner for pools or tanks.
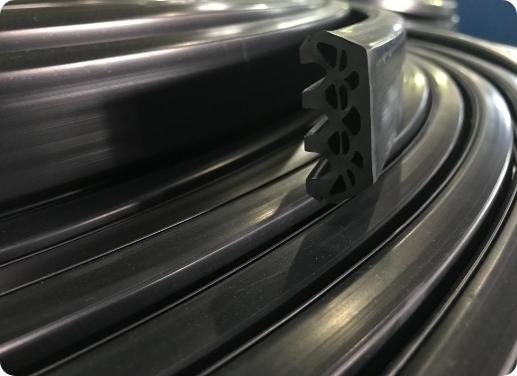
HVAC
EPDM is useful for heating/cooling systems and can be used for tubes, seals, gaskets, and insulation.
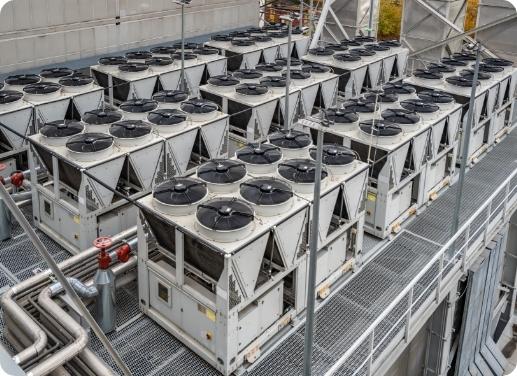
Automotive
It is used for door seals, window seals, trunk seals, and sometimes hood seals, other vehicle uses include wiper blades cooling system circuit hoses, water pumps, thermostats, EGR valves, EGR coolers,
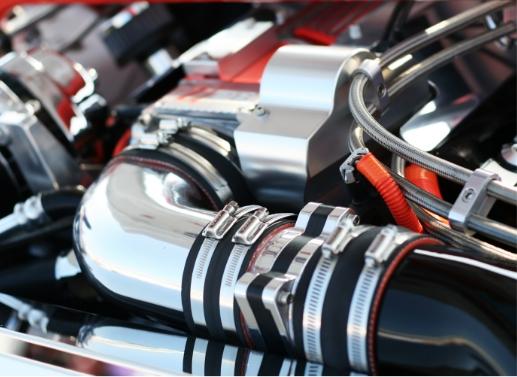
Industrial
EPDM: the go-to material for electrical insulation and waterproofing. From water systems to cables and wires, it seals and insulates. Its elasticity shines in bungee cords, tie-downs, and exhaust system hangers. Plus, it cushions and protects appliances, machinery, and equipment.
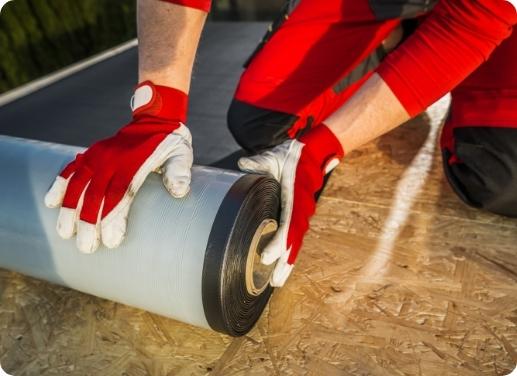
Misc Applications
EPDM is also used in heaters, oil coolers, radiators, and degas bottles connected with EPDM hoses. EPDM is also used as charge air tubing on turbocharged engines to connect the cold side of the charge air cooler (intercooler) to the intake manifold.
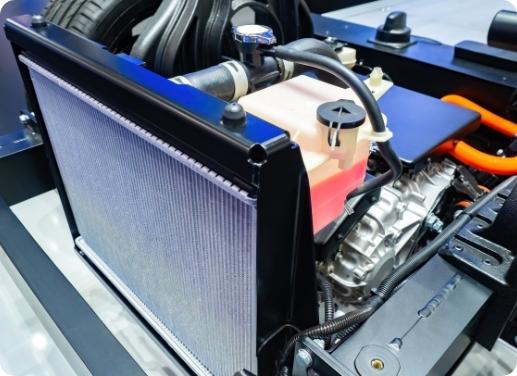